
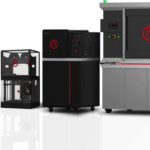
MetalFuse
The mechanical properties of FFF printed parts are fully compliant with MIM quality standards and even slightly exceed them; therefore, they can be used as end parts:
- Description
- Reviews (0)
Description
Raise3D MetalFuse system is comprised of the desktop metal 3D printer Forge1, the catalytic debinding furnace D200-E, the sintering furnace S200-C, the slicer ideaMaker Metal, and uses Ultrafuse® Metal Filaments from BASF Forward AM.
ideaMaker Metal is a modified version of ideaMaker optimized for the use of Ultrafuse® Metal Filaments, with unique features that provide the required part density and repeatability to create end parts of the highest quality.
The sinter D200-E uses an oxalic acid catalytic debinding process, traditionally used by MIM technology, which is safe and environmentally friendly.
According to Raise3D’s internal analysis, excluding parts with a very simple design, the Raise3D MetalFuse solution produces parts with better quality and a lower cost, particularly for small batches, than AM metal laser sintering solutions in the market.
Advantages of FFF vs. MIM
FFF technology allows for full design freedom, which makes possible the production of complex parts that would otherwise be too expensive, or could not be produced, with MIM. This additional design freedom can also allow better mechanical properties of the end parts, which may translate to having FFF as the most cost-efficient technology for metal parts production, even for medium or large batches.
Reviews
There are no reviews yet.